Welcome, Guest |
You have to register before you can post on our site.
|
Online Users |
There are currently 96 online users. » 1 Member(s) | 94 Guest(s) Bing, MikePhua
|
|
|
Liugong CLG990F Excavator — Overview |
Posted by: MikePhua - 06-18-2025, 03:16 PM - Forum: Excavator Specifications
- No Replies
|
 |
The Liugong CLG990F is a large crawler hydraulic excavator designed for mining, heavy earthmoving, and major construction projects. It emphasizes high power output, structural durability, and operational stability. Equipped with a high-performance engine and advanced hydraulic system, it provides customers with an efficient, reliable, and cost-effective solution for the most demanding jobs.
CLG990F Key Specifications (List)
1️⃣ Dimensions- Overall length (transport): 13,210 mm
- Overall width (transport): 4,410 mm
- Overall height (transport): 4,945 mm
- Minimum ground clearance: 880 mm
- Track length: 6,320 mm
- Track shoe width: 650 mm
- Total track width: 4,410 mm
- Upperstructure width: 3,600 mm
- Tail swing radius: 4,400 mm
2️⃣ Working Range- Max digging height: 12,340 mm
- Max dumping height: 8,100 mm
- Max digging depth: 7,830 mm
- Max vertical digging depth: 5,330 mm
- Max digging radius: 11,800 mm
- Min swing radius: 5,050 mm
3️⃣ Performance- Operating weight: 90,000 kg
- Standard bucket capacity: 4.5 m³
- Max digging force (arm): 370 kN
- Max digging force (bucket): 480 kN
- Travel speed: 3.2 / 2.2 km/h
- Swing speed: 6.8 rpm
- Max drawbar pull: 658 kN
- Gradeability: 35°
4️⃣ Engine- Engine model: Cummins QSK19
- Rated power: 447 kW @ 2000 rpm
- Displacement: 19 L
- Cylinders: 6 in-line
- Max torque: 2508 Nm
5️⃣ Hydraulic System- Main pump: 2 variable displacement piston pumps
- Max flow: 2 × 480 L/min
- Main control valve: multi-way valve
- Pilot system: load sensing
- Travel motors: 2 units
- Swing motors: 2 units
6️⃣ Capacities- Fuel tank: 1,250 L
- Hydraulic tank: 550 L
- Coolant: 85 L
- Engine oil: 75 L
- Swing gearbox: 2 × 12 L
- Travel gearbox: 2 × 20 L
Summary
As a mining-class large excavator, the Liugong CLG990F boasts high power, strong digging force, and a large bucket capacity. It delivers exceptional performance for heavy-duty earthmoving and tough mining operations. With industry-leading configurations for power, structure, and hydraulics, it balances strength with fuel efficiency, making it an ideal choice for mining companies and large-scale infrastructure projects seeking reliable high productivity.
|
|
|
Exploring the Gap Between China and Developed Countries in the Excavator Industry |
Posted by: MikePhua - 06-17-2025, 03:06 PM - Forum: Operator Talking
- No Replies
|
 |
Today, I’d like to open up a discussion about some key differences between the excavator industry in China and in developed countries, especially in Europe and North America. These differences are real and highlight the areas where China’s industry still has room to grow. By recognizing this gap, we can find motivation to keep improving and help China’s excavator sector reach a more advanced level.
1. Who Owns the Excavators
In developed countries, most excavators are owned by companies — ranging from large contractors with thousands of machines to small businesses with just a few units. These companies are officially registered, issue invoices for their work, and pay taxes accordingly. In addition, some households own small excavators for personal projects, like digging a backyard swimming pool or laying pipes in a residential area. Many mini excavators in these countries are bought for private use and sit idle when not needed.
In China, by contrast, most excavators are owned by individuals or family-run businesses. Some owners have dozens of machines, but many have just one or two. Often, these owners operate without registering a company or paying taxes on their income.
2. Operator Age and Wages
In developed countries, excavator operators tend to be older, often in their 30s or 40s. This is partly because infrastructure development peaked decades ago, so operators have been trained for many years. Pay and benefits are also relatively good: besides hourly wages, operators usually receive full insurance, pension contributions, and housing benefits. For example, in Tennessee, USA, an excavator apprentice typically earns about $15 per hour, an operator with five years of experience earns around $27 per hour, and a highly experienced operator with over 15 years can earn $45 per hour.
In China, operators are usually much younger, often between 18 and 25 years old. Many were born after 1985 and now form the backbone of the workforce. Wages vary by region but generally range from 2,000 to 4,000 RMB per month. Apprentices often earn nothing at first and sometimes even have to pay their mentors for training. Only a small number of highly skilled operators earn 5,000 RMB or more per month.
3. Appearance and Condition of Excavators
Excavators in developed countries usually look newer and better maintained than those in China. There are a few reasons for this. First, job sites abroad are generally less harsh. Second, operators abroad often choose the right machine size and type for each task. Third, there is a strong habit of regular maintenance and cleaning.
In China, however, it is common for machines to work nonstop, sometimes 24 hours a day. Operators may push a small 2-ton machine to do the work of a much larger one, or use a 20-ton excavator to awkwardly handle jobs better suited for a mini excavator. Many operators also neglect cleaning and maintenance. This misuse and overwork can make machines look much older than they really are.
4. Personalization and Machine Culture
In developed countries, a mature market for excavators has given rise to a culture of personalization. It’s common to see brightly colored excavators on city streets, customized with unique paint jobs requested by their owners. Many operators also add personal touches to their machines, turning them into a reflection of their personality and pride in their work.
In China, customized paint or decals are still rare. Most excavators look the same, and even unusual colors are often seen only on imported second-hand machines. However, there is growing interest among Chinese owners in adding personal touches to their machines, signaling a budding culture of machine pride and identity.
5. Attachments and Tools
Photos of construction sites abroad show that foreign operators use a wide variety of attachments — even buckets alone come in many shapes and sizes, each suited for specific conditions. Specialized attachments help operators work more efficiently and safely.
In China, attachments are still mostly limited to standard buckets and hydraulic breakers. It’s common for an excavator to have just one bucket type, regardless of the task. Other attachments are rarely used, partly because operators and owners are less familiar with them and the market for them is not yet mature.
6. Excavator Transport
In developed countries, excavators are transported on trailers that meet strict safety and environmental standards. These trailers are usually top-quality brands like Mercedes-Benz, Volvo, MAN, or Scania, and seeing them on the road is quite impressive.
In China, large excavators are usually moved on dedicated trailers too. However, especially in rural areas, it’s common to see small excavators transported on modified vehicles, such as farm tractors converted into makeshift trailers. While these are cheap and practical, they often fall short in appearance and environmental compliance.
Conclusion
In summary, there is still a considerable gap between China’s excavator industry and that of developed countries. Much of this difference stems from historical factors, but it also highlights the work that remains to be done. As China’s national strength continues to grow, there is every reason to believe that the excavator industry will keep improving and eventually match global standards.
|
|
|
The Steam Shovel: The Pioneer of Earthmoving Machinery |
Posted by: MikePhua - 06-17-2025, 03:00 PM - Forum: Operator Talking
- No Replies
|
 |
When we talk about earthmoving machinery today, images of massive excavators, bulldozers, and mining shovels often come to mind. But few people know that the roots of these powerful machines trace back nearly two centuries — to a remarkable invention known as the steam shovel.
A Humble Beginning in the Age of Steam
By its nature, earthmoving equipment is a specialized category within the broader world of heavy machinery. Unlike locomotives or ships, it rarely grabs headlines, and historically, its development has often relied on technologies borrowed from other sectors — especially transportation.
Structurally, earthmoving machines can be divided into three main systems:- The power system, which drives all motion;
- The undercarriage or traveling system, which moves the machine;
- The working implement, which actually digs, pushes, or lifts material.
While the working implement often requires unique industry-specific design, the power and mobility systems have long been technological bottlenecks, dependent on advances in engines and mobility solutions developed for other industries.
The Industrial Revolution Sets the Stage
The Industrial Revolution transformed how humans worked. After the steam engine was invented, it first powered textile factories, then revolutionized transportation. In 1825, the world’s first railway opened in Britain, and by 1830, the United States built its own rail line.
These new railways created an enormous demand for earthworks — vast quantities of soil and rock had to be moved to lay tracks through hills and valleys. This challenge led to a key invention that would change earthmoving forever.
William Otis and the Birth of the Steam Shovel
In 1835, William Otis, a young railway contractor in Philadelphia, invented the steam shovel to tackle large excavation jobs more efficiently than manual labor ever could. He secured a patent in 1839 — just four years before his untimely death at age 26.
Otis’s steam shovel was ingenious for its time. Its design featured a crane-like mast and boom with a bucket arm (dipper) mounted at the end. A steam engine powered a winch system of chains and pulleys to lift or lower the bucket, while gears moved the arm in and out. Workers helped swing the boom and control the bucket latch. The entire apparatus sat on a four-wheeled rail car. By laying rails ahead of the shovel, it could excavate a trench in stages — a method well-suited to railway construction. This early machine became known as the “railway shovel.”
Though primitive by modern standards, Otis’s invention was groundbreaking: it was the first time a machine replaced human hands for large-scale digging. Before bulldozers and scrapers appeared in the 1920s, “earthmoving machinery” basically meant steam shovels.
Early Challenges and Gradual Improvements
The first Otis “Philadelphia” shovel began working on a railway project in 1837. Sadly, Otis passed away before he could refine his design, and production stalled for years. It was not until the 1850s that his family revived manufacturing, though output remained limited.
Early steam shovels were far from perfect:- Their swing range was limited and partly manual.
- Steam engines were underpowered, so digging force and bucket capacity were modest.
- Frequent coal and water refills were needed.
- Workers had to keep laying new tracks to reposition the machine.
Despite these shortcomings, the idea caught on. After Otis’s patent expired, new companies entered the market. By the 1870s, growing demand for large earthworks — from railways to canals and mines — sparked rapid innovation. Manufacturers popped up in the U.S. Great Lakes region, Britain, and Germany.
Powering Iconic Projects
By the late 19th century, steam shovels had become essential tools for mega projects. They were used extensively to dig the Manchester Ship Canal and later played a decisive role in constructing the Panama Canal in the early 20th century, helping the U.S. succeed where the French had failed.
A typical jobsite scene from this era featured steam shovels operating on rail tracks, with small dump cars lined up alongside to carry away spoil. These cars were hauled by humans, horses, or steam locomotives.
Evolving with New Demands
To overcome early limitations, engineers kept improving the steam shovel’s design:- Steam engines grew more powerful.
- Booms and dipper arms became longer.
- Buckets increased in size, and machines became bigger and heavier overall.
Flexibility was another challenge. Early models could not swing freely in any direction. A full 360-degree swing mechanism was invented in Britain in the 1880s but only became widespread in the 1920s. Heavy machines still faced limits due to the massive weight of steam boilers.
Another leap forward was freeing shovels from railway tracks. Self-propelled steel wheels came first, followed by crawler tracks — the ancestors of modern excavator undercarriages. Some large steam shovels even used four crawler tracks for stability. Unlike the chain tracks developed by Holt (the forerunner of Caterpillar), most steam shovels used pin-connected tracks.
Legacy and Transformation
By the 1920s, steam shovels had reached their technological peak. Apart from the steam power source, their structure was nearly identical to modern electric mining shovels. But the era of steam was coming to an end.
As internal combustion engines became widespread in vehicles, tractors, and bulldozers, steam shovels gradually transitioned to gasoline engines, then diesel, and eventually to diesel-electric or fully electric drives. Still, steam-powered models continued to be produced into the 1930s, and some stayed in service as late as the 1950s.
A Lasting Impact
Looking back, the steam shovel was far more than just an early digger — it laid the groundwork for today’s heavy-duty earthmovers and giant mining shovels. It turned an exhausting manual job into a mechanical process and opened new possibilities for modern engineering and mining.
From William Otis’s modest rail-mounted machine to today’s towering electric mining shovels, the steam shovel’s legacy lives on in every bucket that bites into the earth.
If you’d like, I can help turn this into a polished blog post, add images, or make a nicely formatted PDF version. Just say the word!
|
|
|
A User’s Experience with a SANY SY330 Excavator |
Posted by: MikePhua - 06-17-2025, 02:56 PM - Forum: Operator Talking
- No Replies
|
 |
On March 17, during the peak sales season for excavators in the first half of the year, I purchased a SANY SY330 excavator. After putting it to work, I began to notice several problems.
When I first received the machine, I immediately felt that the operation was not smooth. The movements were sluggish and jerky. At first, I thought the problem was due to the operator being unfamiliar with the new machine, so I didn’t pay much attention to it. However, after a week, the issues persisted. The boom and arm were particularly slow — raising the boom at a horizontal position took more than 10 seconds, and fully extending or retracting the arm took over 6 seconds. Doing leveling work was painfully slow: leveling a 20-meter stretch of road could take half an hour or longer. I called the service technicians, but they couldn’t fix the problem.
By the time the machine had run for 200 hours, the service team had come six times but still hadn’t resolved the issue. The machine’s speed sometimes improved temporarily but would slow down again. Later, SANY’s own technicians came and modified the system from negative flow to positive flow. After testing, the performance seemed much better: the boom took about 6 seconds, the arm about 4 seconds, and the bucket about 3 seconds. We thought the problem was finally solved — the technicians even set off firecrackers to celebrate. But the improvement only lasted for three days before the machine slowed down again, although it was slightly better than before.
Now, with over 600 hours on the machine, the problem still hasn’t been properly resolved. The dealer’s service staff have visited about 20 times and driven almost 8,000 km just for my machine. They even bought a new service vehicle because of these frequent trips. However, nothing has really changed, so I have no choice but to keep using the excavator as is, hoping that the manufacturer or dealer can eventually fix it properly.
Here is a summary of the issues I have encountered with this SANY SY330:
- Slow and uncoordinated operation, very poor control performance.
- Power cannot be fully shut off: when the key is removed, the power remains on. (This has since been fixed.)
- Bucket teeth cannot be replaced easily: each time, the tooth pins get stuck and have to be cut with an oxy-acetylene torch. So far, I have replaced four sets of teeth and had to torch ten pins, costing about 1,000 RMB each time. All the teeth and pins are genuine parts purchased from SANY.
- The pin connecting the boom and arm has a retaining plate, but this plate once fell off because it wasn’t welded securely. The pin slid halfway out — if I hadn’t noticed in time, the arm could have fallen off completely.
- Doors on the battery box and hydraulic pump box have broken pins; the cabin door latch has also broken.
- When using the heater, there is a burning plastic smell inside the cab, and the cabin is very noisy. Even though the machine is new, it shakes and rattles like an old one.
- The work light is poorly positioned and cannot be adjusted.
- The machine lacks power under load: whenever there is pressure, it belches black smoke, similar to the smoke at startup, and this happens frequently. When starting in the morning, it emits blue smoke for about 10 minutes. The service staff claim this is normal.
Due to these issues, I sincerely hope that SANY’s management and design team can pay attention and resolve these problems promptly. The downtime and low efficiency have already caused significant delays and increased my operating costs, which I can hardly afford anymore. I also hope this feedback can serve as a reference for others who are considering purchasing an excavator. Thank you.
|
|
|
Asphalt Transfer Vehicles in China: On Pause or in Shock? |
Posted by: MikePhua - 06-17-2025, 02:54 PM - Forum: Operator Talking
- No Replies
|
 |
An Imported Technology
Asphalt transfer vehicles (ATVs) were first developed in the United States in the 1990s. Their proven success in the American market quickly caught the eye of savvy equipment dealers, who began actively promoting them to Chinese customers around the year 2000. However, ATVs have experienced a rather bumpy journey in China.
Early promotional efforts failed to open up the Chinese market. It wasn’t until October 2002 that things began to change. That year, Hebei Road & Bridge Group purchased a ROADTEC SB-2500B asphalt transfer vehicle through Beijing Rongshijie Company and deployed it on the Hangzhou Ring Expressway. This marked China’s first imported asphalt transfer vehicle. The machine attracted widespread attention on site and sparked considerable buzz in the industry.
Around the same time, SANY Heavy Industry launched its own research and development program for asphalt transfer vehicles under China’s national “863” high-tech plan. By September 2002, SANY had unveiled its LHZ25A model at the 6th Highway and Waterway Transportation Expo.
From then on, ATVs became a hot topic in China’s road construction sector.
A Rising Star That Faded
Following this wave of attention, both domestic and international manufacturers rolled out their own models. However, controversy has surrounded ATVs ever since. Objectively speaking, they do help improve paving quality. But convincing Chinese customers to adopt such an expensive auxiliary machine has proven difficult.
Compared to the bustling market scene just three or four years ago, today’s ATV market in China is eerily quiet. What happened? Is the industry calmly biding its time, or has it fallen into a deep coma due to entrenched construction practices and economic realities?
Luxury or Necessity?
In essence, an asphalt transfer vehicle is an auxiliary device: it is a sufficient but not necessary condition for high-quality pavement construction. Put simply, roads can be built perfectly well without it. So a machine that costs three to four million RMB but only provides incremental improvement is understandably a tough sell.
There has long been debate about whether ATVs make sense for China’s highway construction. While no one disputes their technical benefit, the real issue is whether they offer value for money given local conditions.
It’s worth noting that ATVs have seen consistent use in only a few regions, such as Inner Mongolia. This is partly due to the region’s long, narrow geography and large diurnal temperature swings, which make material segregation more likely. It’s also because local road authorities and project owners there specifically require ATVs and support their use through policy incentives.
For the rest of China, however, whether this paving method is suitable, cost-effective, and ultimately worthwhile still needs to be validated with hard data and long-term performance results.
Driving Change or Hitting a Bottleneck?
In China, several industry characteristics have hindered the widespread adoption of ATVs: tight cost controls, suboptimal equipment combinations, and the fragmented scale of road contractors. Many contractors own minimal equipment to maximize profit margins. As a result, investing in an expensive auxiliary machine is not a priority.
In Europe and the U.S., centralized batch plants are designed with environmental considerations in mind, and contractors often haul asphalt mixes over distances of more than 100 kilometers. In this context, transfer vehicles play a critical role in preventing temperature drops and material segregation during long hauls. Large contractors handle extensive paving mileage and are also responsible for long-term road maintenance, so any improvement in pavement durability directly benefits them financially.
In contrast, Chinese contractors typically have their own on-site mixing plants positioned within each 20–30 km section. Transport distances are short, so asphalt temperature drops only slightly (usually 3–5°C), and segregation is minimal. Asphalt is discharged directly from trucks into the paver, leaving little room for transfer vehicles to add value. This has led some to dismiss ATVs as redundant.
Breaking the Deadlock
Regardless of whether they support or doubt ATVs, most industry insiders agree on one thing: the technology works. The real debate is whether it delivers a good return on investment under China’s unique construction model.
Interestingly, at the 2004 Bauma China trade fair, even traditionally conservative European brands like Wirtgen’s Vögele and Sweden’s Dynapac surprised the industry by launching new ATV models (the MT1000-1 and MF250, respectively). This made it clear that debating regional paving methods had become irrelevant—transfer vehicles are part of the global trend and an important technology reserve.
So where does the problem lie in China? Owners and investors calculate carefully: will the long-term savings in maintenance offset the upfront cost of an ATV? Only time will tell. But a three- to four-million-RMB price tag certainly makes buyers hesitate.
China’s revised Technical Specifications for Highway Asphalt Pavement Construction now mention ATVs explicitly. Section 5.5.4 states:
Quote:“...When conditions allow, delivery trucks may unload asphalt mixes into a transfer vehicle for secondary remixing and continuous, uniform feeding of the paver...”
That phrase “when conditions allow” implicitly acknowledges the high cost barrier.
Future Prospects
Despite the recent lull, the trend towards continuous paving with ATVs is clear. Leading global brands now promote double-layer hot paving technology as the next big thing. In China, domestic players like XCMG, SANY, Dingsheng Tiangong, and Xinzhu have all joined the market with their own products.
As one industry expert bluntly put it:
Quote:“The benefits of ATVs are real, but some manufacturers overhype them—leading to disappointment. This reflects the restless, hype-driven mindset that still plagues parts of China’s construction machinery industry.”
Recent market quietness has tested ATV makers, forcing them to adapt and design models better suited to Chinese conditions. Some signs of recovery have already emerged: for instance, XCMG recently delivered three new ATVs, and a company representative told reporters that the market is entering another cycle of growth.
Summary
The asphalt transfer vehicle in China is neither dead nor fully alive—it stands at a crossroads. With better cost control, data-backed performance, and an evolving construction environment, ATVs are likely to earn their rightful place in China’s road-building arsenal.
|
|
|
Introducing New Equipment: The Glory and Struggles of Scrapers |
Posted by: MikePhua - 06-17-2025, 02:51 PM - Forum: Operator Talking
- No Replies
|
 |
A Century of Development
The scraper, a key piece of earthmoving machinery, has been evolving for over a century. As early as the 18th century, horse-drawn scrapers were used for short-haul soil transport. By 1883, the first fully metal-wheeled scraper was manufactured in the West.
In 1910, the United States built dedicated scrapers towed by tractors, while the Soviet Union began mass-producing wheeled scrapers in the 1920s. By 1938, the world saw its first self-propelled scraper, followed by twin-engine and chain-loader variants in the mid-20th century—culminating in the 1960s with the world’s largest scraper, boasting a 200 m³ bowl capacity.
China entered the scraper field in the 1960s. In April 1961, several institutions—including the predecessors of Yutong Heavy Industries, Tianjin Research Institute, and XGMA—formed a joint design team. Drawing on imported prototypes, they developed China’s first self-propelled scraper. The design was completed that August, and on December 22, 1962, the first prototype (C-6106) rolled off the line in Zhengzhou.
Scrapers: Built for Efficiency
Scrapers are unique in that they combine cutting, loading, and hauling in a single machine. They shine in medium-haul applications—roughly 200 to 1,200 meters—where they outperform the typical excavator–loader–dump truck combination in both speed and cost-effectiveness.
Recognizing this, China invested heavily in scraper research during the 1960s and 1970s. The CL7 model, trialed in 1972, adopted advanced hydro-mechanical transmission and full hydraulic control. It marked a major technical leap, earning a National Science and Technology Award in 1978 and even showcasing China’s progress at the 1975 Cologne International Fair in Germany. In 1978, two CL7 scrapers were used in a groundbreaking test on the Qinghai-Tibet Railway—China’s first industrial field trial for high-altitude road construction equipment.
A Legacy Now Struggling
Fast forward several decades: despite their engineering advantages, scrapers are now nearly phased out in China. Their work has been almost entirely replaced by flexible excavator-loader-dump truck combinations. By contrast, scrapers still handle around 40% of total earthwork in the United States.
Why has China’s scraper industry lagged behind after more than 40 years?
The Subcontracting Dilemma
Take the massive South-to-North Water Diversion Project as an example: planners calculated that 700 scrapers would be needed to tackle over 830 million cubic meters of earthwork. Yet in reality, scrapers were almost absent from the project site, despite engineers insisting they were the most efficient option.
The root cause lies in China’s subcontracting system. Scrapers are more specialized than excavators or dump trucks, and cost more upfront. For a 400-meter haul, two self-propelled Caterpillar scrapers can match three excavators and nine dump trucks. But tight profit margins and higher equipment costs make small to mid-sized subcontractors reluctant to invest in scrapers—especially given their narrower range of applications.
Even long-time scraper proponents like China Railway Construction Corporation face an uphill battle promoting them in today’s fragmented subcontracting environment.
Missing Market Drivers
In the 1950s and 1960s, Western embargoes forced China to reverse-engineer foreign machines. By the late 1960s, both a ZL45 loader and a chain-type twin-engine scraper were secretly acquired and copied. Decades later, loaders are now ubiquitous, dominating the construction machinery market. Meanwhile, scrapers are nearly forgotten—except for isolated success stories like the Holingol coal mine in Inner Mongolia, where shallow seams made scrapers highly profitable.
The lesson? Markets don’t build themselves. While only Yutong Heavy Industries persisted in scraper production, one company alone cannot nurture demand. Scrapers are more technically challenging to build than loaders, and without a strong market, few manufacturers are willing to invest.
A Path Forward
The dilemma is clear: no market means no manufacturers, and no manufacturers means no market. In fact, the construction machinery industry must take the lead in educating customers about modern, efficient earthmoving methods. Just as loaders gained popularity through joint effort, scrapers too can find their rightful place—especially as specialized contractors grow and labor costs continue to rise.
Caterpillar, which holds 95% of the global self-propelled scraper market, remains confident: despite setbacks, they believe that scrapers will eventually see a revival in China.
Illustration Suggestions
To make this article visually engaging, I recommend these supporting images or diagrams:
- Timeline infographic — showing key scraper milestones: horse-drawn → metal-wheeled → self-propelled → twin-engine → modern large-capacity models.
- Side-by-side comparison diagram — scraper vs. excavator-loader-dump truck combo for the same haul distance.
- Historic photo — early C-6106 prototype at Zhengzhou Plant.
- Modern worksite photo — a scraper in action, ideally a Caterpillar model in the U.S. or at a large open-pit mine.
- Pie chart or bar graph — showing scraper usage percentage in China vs. the U.S.
- Quote highlight box — with Caterpillar’s statement about scrapers’ future in China.
|
|
|
10 Hours with the Liugong 913E — First Impressions |
Posted by: MikePhua - 06-16-2025, 11:22 PM - Forum: Operator Talking
- No Replies
|
 |
I just put in about 10 hours on my brand-new Liugong 913E, and here’s my initial take: - Operation: Overall, the controls feel smooth, the power is decent but nothing impressive, and the speed is on the slower side.
- Modes: I tried out E, P, and F modes, but honestly, the difference between them isn’t very noticeable.
- Fuel Consumption: This is the biggest surprise — it’s really fuel-efficient. I fueled up four drums before starting, plus whatever fuel came in the tank, did around 1,000 cubic meters of earthwork (conservatively estimated), and after 10 hours, the fuel gauge still shows half full. Hard to believe!
- Compared to the old 915D: When my 915D was new, it never went below 9 liters/hour even on light work. The 913E has noticeably lower power, but for light earthmoving on flat ground, it’s actually a perfect match.
|
|
|
Expomina Perú 2026: Unlocking New Mining Opportunities in South America |
Posted by: MikePhua - 06-16-2025, 04:51 PM - Forum: Equipment Market News
- No Replies
|
 |
In the global mining landscape, Peru — the shining jewel of South America — continues to captivate the world with its abundant mineral resources and booming mining sector. From September 9 to 11, 2026, the highly anticipated Expomina Perú 2026, held biennially, will take place at the Lima International Exhibition Center. As one of the largest mining industry events in Peru, it serves as an exceptional platform for global mining companies to explore the South American market, forge trade partnerships, and exchange cutting-edge technologies.
Authoritative Organization with Global Influence
Expomina Perú 2026 is jointly organized by DIGAMMA and the National Society of Mining, Petroleum and Energy of Peru, with strong support from Peru’s Ministry of Energy and Mines, as well as collaboration from leading mining and equipment associations. The event boasts a proven track record of success, having attracted nearly 1,400 exhibitors from countries including the United States, Chile, Canada, Argentina, Mexico, Colombia, Australia, China, Italy, Spain, and Brazil. Over 50,000 professional visitors flock to the show each edition, cementing its global reputation and industry impact. In 2026, it is set to once again gather mining professionals and leaders from around the world and become the focal point of the industry.
A Golden Market Full of Opportunity
Peru, a land rich in untapped treasures, spans 1,285,216 square kilometers, making it the second-largest country in South America after Brazil. Its mineral wealth is truly remarkable, establishing Peru as a mining powerhouse and a top global producer of various mineral commodities.
Peru holds approximately 57.9 million tonnes of copper reserves, accounting for 11.8% of the world’s total, ranking second globally after Chile. Its zinc reserves stand at 18.2 million tonnes (3rd worldwide); lead reserves at 3.5 million tonnes (4.4% of the global total); silver reserves reach 36,000 tonnes (3rd globally); and gold reserves total 3,000 tonnes, representing 8.3% of the world’s supply and also ranking 3rd worldwide — making Peru a key player in the global gold market.
Mining remains a cornerstone of Peru’s economy, with enormous development potential. The Peruvian government actively promotes mining growth through a series of favorable policies covering taxation, foreign exchange, and administrative management, creating a stable and attractive investment climate for companies. This thriving market, coupled with supportive policies, presents vast opportunities for global mining enterprises ready to tap into Peru’s immense potential.
Full Industry Supply Chain, One-Stop Trade Platform
Expomina Perú 2026 will showcase an extensive range of products covering the entire mining industry supply chain. Exhibits will include geological exploration equipment, surveying instruments, various types of wear-resistant steel balls, tunneling, drilling, mining and blasting equipment, as well as mine ventilation, lighting, and safety solutions. Heavy-duty mining trucks, excavators, engineering machinery, electrical equipment, cables and wires, mineral processing chemicals, refractory materials, and welding consumables will also be on display.
Whether you are a manufacturer, supplier, buyer, or technical service provider, you will find precise business partners here, match supply and demand, close trade deals, and drive technological innovation and industry development.
Expomina Perú 2026 — Seize the Opportunity!
Expomina Perú 2026 is more than just an opportunity; it is a gateway to the dynamic South American mining market. Join us to expand your market reach, build new partnerships, and achieve new success on this promising land. Exhibition spaces are limited and opportunities wait for no one — secure your spot now to gain an edge, be part of this grand mining event, and embark on your new journey to prosperity!
|
|
|
Yonggong YGX360LC-8 excavator Specifications |
Posted by: root - 04-26-2025, 01:55 AM - Forum: Excavator Specifications
- No Replies
|
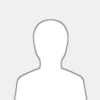 |
The Yonggong YGX360LC-8 crawler coal unloading excavator is a large-scale machine designed specifically for coal handling operations. It is known for its efficiency, durability, and reliability. Below is the detailed information :
Overview
The Yonggong YGX360LC-8 crawler coal unloading excavator features an advanced hydraulic system and a powerful engine, ensuring excellent performance in demanding work environments. Its design emphasizes operator comfort and equipment durability, making it ideal for coal transportation and mining operations.
Specifications
- Operating Weight: 33,500 kg
- Bucket Capacity: 2.5–3.0 m³
- Rated Power: 118 kW / 2,200 rpm
- Boom Length: 6,000 mm
- Stick Length: 3,500 mm
- Swing Speed: 12 rpm
- Travel Speed: 0–4.5 km/h
- Gradeability: 56%
- Maximum Traction Force: 180 kN
- Main Relief Pressure: 34 MPa
- Maximum Pump Flow: 2×212 + 30 L/min
- Hydraulic Tank Capacity: 245 L
- Fuel Tank Capacity: 240 L
- Transport Length: 10,085 mm
- Transport Width: 3,200 mm
- Transport Height: 4,200 mm
- Maximum Digging Height: 5,815 mm
- Maximum Digging Radius: 8,640 mm
Summary
The Yonggong YGX360LC-8 crawler coal unloading excavator is an excellent choice for coal handling tasks, thanks to its efficient hydraulic system, powerful engine, and flexible operation. It enhances productivity while reducing operational costs, making it a reliable partner for heavy-duty work.
|
|
|
The Chongqing QN3700 excavator Specifications |
Posted by: root - 04-26-2025, 01:53 AM - Forum: Excavator Specifications
- No Replies
|
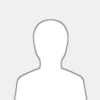 |
The Chongqing QN3700 long-arm excavator is a specialized crawler excavator designed for unique working conditions. With its extended boom and stick, it is ideal for tasks such as building demolition, river dredging, and deep trench excavation. Below is the detailed information in English:
Overview
The QN3700 long-arm excavator features a two-section extended boom design, with a boom length of 12 meters and a stick length of 9 meters, totaling 21 meters. This design significantly enhances its digging height, depth, and radius, enabling it to handle tasks that standard excavators cannot. It is suitable for applications such as soil and concrete handling, building demolition, subway excavation, highway slope trimming, and river dredging.
Specifications
- Operating Weight: 37,000 kg
- Rated Power: 187 kW / 1,950 rpm
- Boom Length: 12 m
- Stick Length: 9 m
- Total Length: 21 m
- Applications: Specialized working conditions
- Suitable Scenarios: Building demolition, river dredging, deep trench excavation, etc.
Summary
The Chongqing QN3700 long-arm excavator is an excellent choice for specialized tasks, thanks to its extended working range and powerful performance. Its flexibility and efficiency make it a standout performer in construction, river management, and other fields, offering reliable solutions for challenging projects.
|
|
|
|